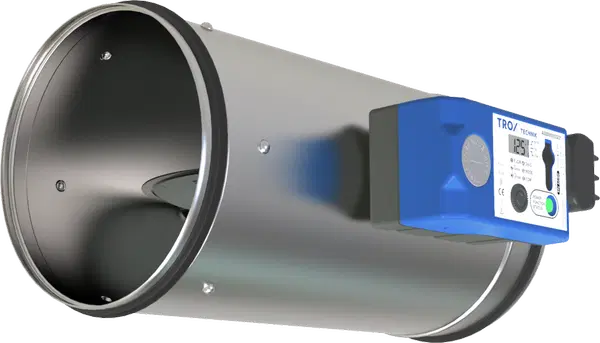
Circular air terminal units for use in variable air volume systems at low airflow velocities, even under unfavourable upstream conditions
Optional equipment and accessories
Application
Special features
Nominal sizes
Variants
Construction
Parts and characteristics
Attachments
Accessories
Useful additions
Construction features
Materials and surfaces
Galvanised sheet steel
Powder-coated construction (P1)
Stainless steel construction (A2)
Acoustic cladding
Mineral wool
Standards and guidelines
Fulfils the hygiene requirements of
Casing leakage
Closed blade air leakage:
NS 100 – 160
NS 200 – 400
Maintenance
Product Information
Brochures
Certificates
Operation Manuals