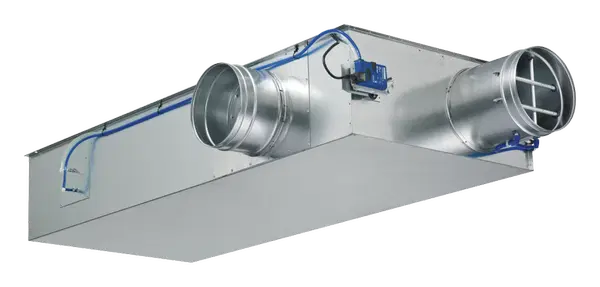
VAV dual duct terminal units for dual duct systems with variable volume flows in buildings with demanding acoustic requirements
Optional equipment and accessories
Application
Special features
Nominal sizes
Variants
Parts and characteristics
Attachments
Accessories
Useful additions
Construction features
Materials and surfaces
Variant with acoustic cladding (-D)
Mineral wool
Standards and guidelines
Fulfils the hygiene requirements of
Casing leakage
Closed blade leakage
Nominal sizes 125 and 160
Nominal sizes 200 to 400
Maintenance
Product Information
Certificates
Operation Manuals